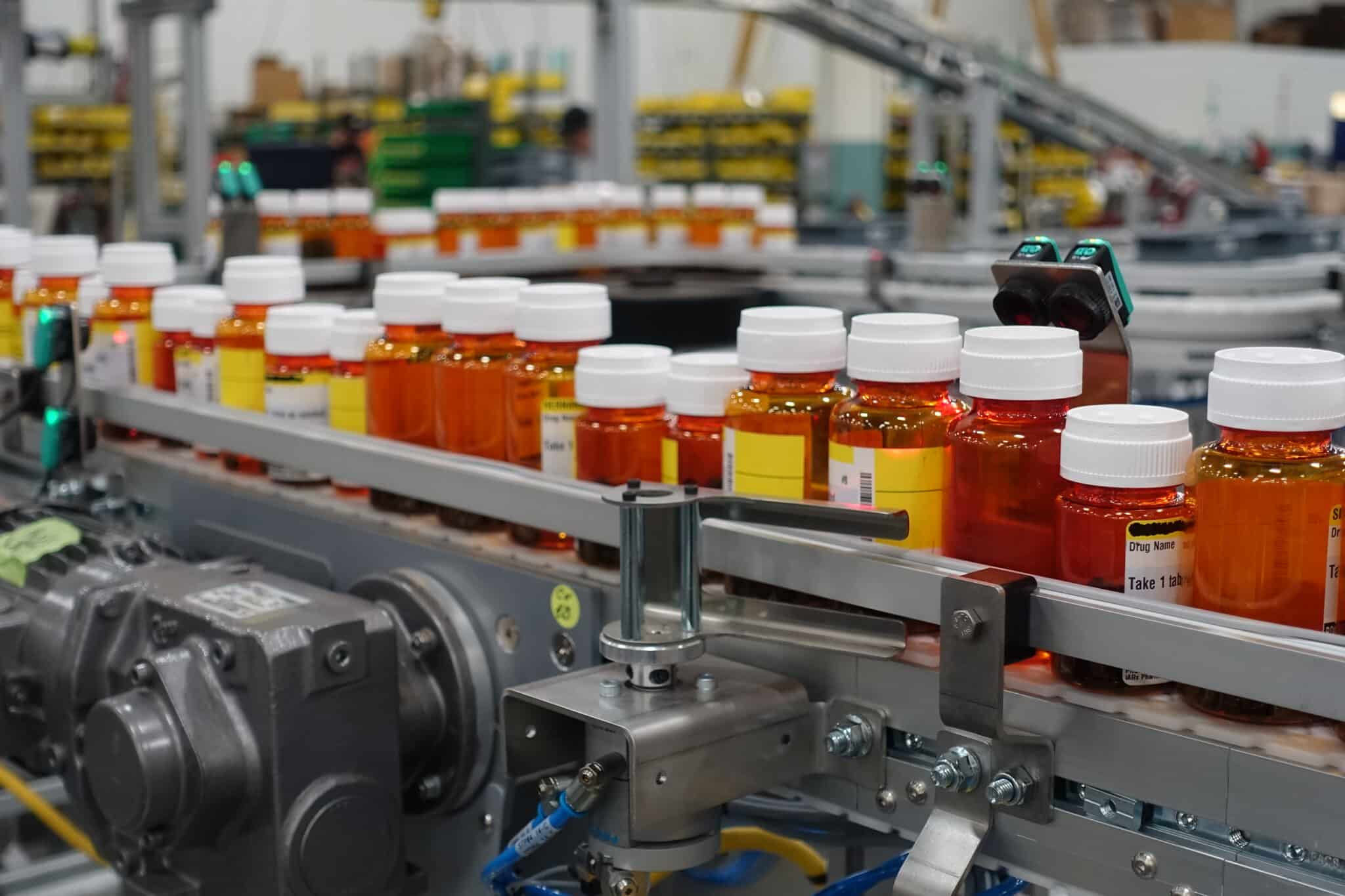
The pharmaceutical industry has endured systematic changes in the last ten years due to challenges such as regulatory changes, cost pressures, and accuracy.
These changes have led pharmaceutical leaders towards investment in automated conveyor systems. These systems provide agility and adaptability to production, packaging, and fulfillment operations to improve traceability, quality control, contamination control, and cost & production efficiency. At the highest level, a conveyor is a tool to move product from point A to point B; however, the depth of detail required to transport pharmaceutical products from beginning to end requires a much more specific solution.
Government Regulations
The specificity of a pharmaceutical conveyance solution starts with the regulations and standards that a manufacturing operation must follow. One of the critical regulatory standards that pharmaceutical manufacturers use is the Current Good Manufacturing Practices (cGMPs). cGMP regulations outline the minimum requirements for designing, monitoring, and controlling pharmaceutical manufacturing processes. These requirements cover facility design, equipment qualification, documentation, process validation, quality control testing, and record keeping.
Conveyance solutions used in pharmaceutical manufacturing must adhere to stringent government regulations and industry standards. The specific requirements set forth by regulatory bodies, such as the FDA and ISO certification, are essential for ensuring product safety, quality, and compliance. Conveyors used in pharmaceutical plants are subject to rigorous testing and must meet specific criteria for cleanrooms*, which maintain strict cleanliness and sterility levels to prevent contamination.
Dorner, a trusted provider of conveyor solutions, offers a range of pharmaceutical conveyors designed to meet the various sanitary and functional levels required by different applications. By investing in conveyors that comply with government regulations, pharmaceutical manufacturers can ensure the integrity of their production processes, minimize the risk of regulatory penalties, and maintain a strong reputation for producing safe and effective pharmaceutical products. These compliance-driven conveyance solutions provide peace of mind and contribute to the overall success and profitability of the pharmaceutical plant.
Cost Pressures
Pharmaceutical production plants face significant cost pressures due to various factors, such as the rising demand for medications, stringent regulatory requirements, and increasing competition. Implementing the right conveyor system can help mitigate these costs.
Conveyors are crucial in moving raw materials, intermediates, and finished products throughout the manufacturing plant. By optimizing material flow and reducing manual handling, conveyors can enhance productivity, minimize labor costs, and prevent errors or contamination.
Space is continuously an issue for growing businesses. The right conveyor solution can maximize space utilization, allowing for streamlined layouts and increased production capacity without additional floor space. In addition to maneuvering small footprints, automated conveyors with advanced monitoring and control systems offer improved traceability, quality control, and adherence to regulatory standards, reducing the risk of costly product damage or compliance issues.
Additionally, conveyor solutions are pivotal in enhancing pharmaceutical plant ergonomics, effectively alleviating cost pressures and boosting profits. By integrating automated conveyor systems into the production process, pharmaceutical plants can significantly improve the overall ergonomics of their operations.
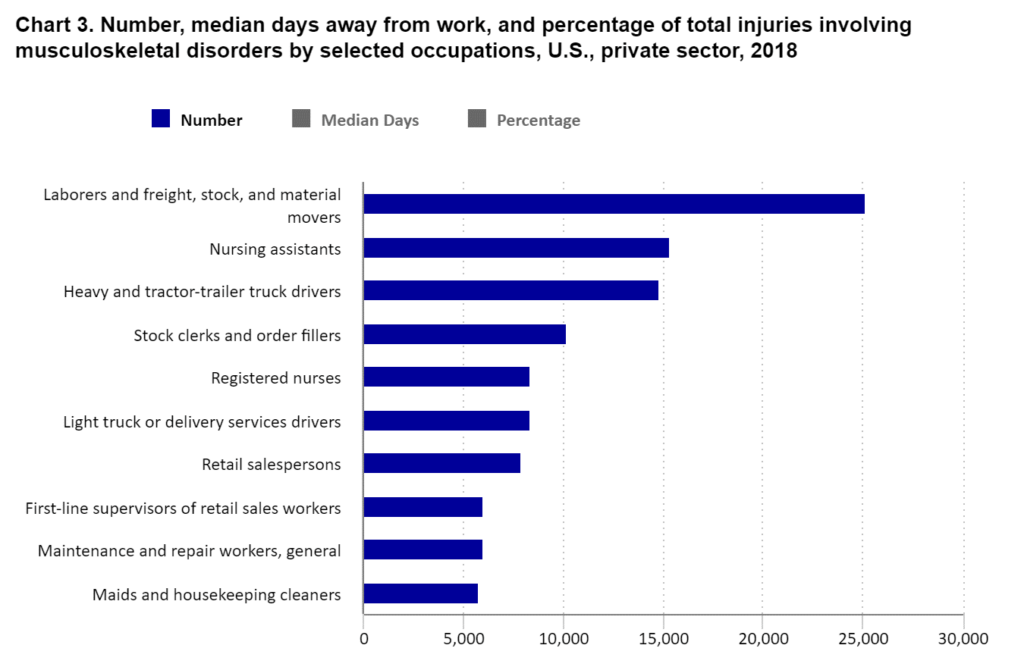
https://www.bls.gov/iif/factsheets/msds.htm
In 2018 private sector laborers, freight, stock, and material movers had 25,110 musculoskeletal disorders such as carpal tunnel, tendinitis, muscle strains, and lower back injuries. The rate of these types of injuries is reduced through the use of conveyors that streamline material handling, eliminating the need for manual lifting, carrying, and repetitive motions that can lead to injuries and worker fatigue. By reducing physical strain on employees, conveyor systems enhance worker safety and well-being, lowering absenteeism rates and increasing productivity.
Furthermore, these automated solutions optimize workflow efficiency, minimizing downtime and product handling errors. The streamlined processes facilitated by conveyor systems enable pharmaceutical plants to achieve higher production volumes, faster turnaround times, and improved product quality. As a result, companies can meet market demands more effectively and maintain a competitive edge, ultimately leading to increased profits and long-term business growth.
Accuracy
Conveyors play a vital role in enhancing accuracy within pharmaceutical production processes. They ensure consistent and controlled movement of materials reducing the risk of errors or inconsistencies caused by manual handling. By accurately positioning pharmaceutical products at various stages of production, conveyors minimize the chances of inaccuracies during labeling, packaging, and inspection. Dorner’s multiple conveyance solutions can assist in inspection and testing, rotation, indexing, positioning, merging, diverting, and sorting.
Integrating conveyors with inspection systems enhances accuracy by enabling real-time quality checks. The ERT150 and 250 pallet conveyors offer a lift and locate feature, which lifts the pallet and allows an operator to do their inspection or robotic automation to interact with the product without altering the flow of the conveyor.
As products move along the conveyor, backlit systems and metal detectors can identify defects or contaminants, allowing immediate corrective actions. By reducing reliance on manual handling, conveyors also minimize human error, which can introduce variability and mistakes in the production process. For further checks, conveyors can be integrated with serialization and tracking systems to ensure accurate product traceability of pharmaceutical products to enable precise identification and improve overall quality control.
Dorner offers a range of pharmaceutical conveyors that can be outfitted with accessories and modules to excel in the unique demands of each application. These conveyors are designed to meet the highest standards of performance while meeting government standards and verifications.
Find out more about Dorner’s Pharmaceutical Conveyors
Dorner’s pharmaceutical conveyance solutions are configurable on DTools. Once in DTools, you will have to opportunity to build your ideal conveyor. For further assistance, contact our customer service team here.
*To verify cleanroom requirements, an unloaded base conveyor was tested and did not generate particulate that would be beyond the specified standards. However, the verification does not provide assurance that any or all applications will meet this requirement. Application testing is recommended to ensure clean room standards are being met. Dorner takes no responsibility in the clean room performance of the final conveyor or application.